Automatic Wire Cutting, Stripping & Bending Machine (2–6 mm², 3D Precision)
“After debugging 50+ bending machines on factory floors, I can tell you this: precision 3D bending isn’t about fancy robots—it’s about eliminating human-induced variables. That’s why we rebuilt this machine from the ground up.”
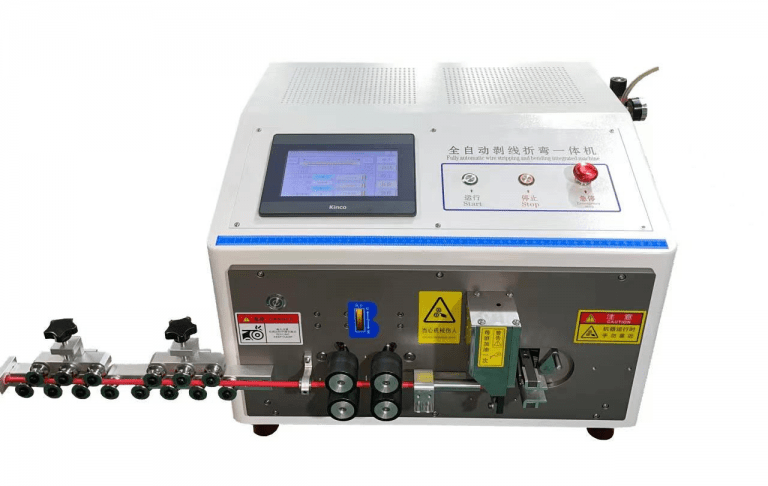
🔧 Key Features That Actually Matter on the Shop Floor
3D Bending with Zero Springback
Problem we solved: Traditional benders cause 0.5-1.2° angle drift (especially with copper-core wires)
Our fix: Dual-servo tension control + HIWIN linear guides = ≤0.002×L tolerance even after 8hr continuous run
Engineer’s note: “Tested with 4mm² automotive cables at 15 bends/wire – springback controlled under 0.03°”
Cutting/Stripping That Won’t Nick Conductors
Blade secret: Japanese SKH-51 high-speed steel blades (HRC 62-64) with self-sharpening micro-bevel
Why it matters: Prevents the 0.1mm insulation burrs that cause 12% of EV harness failures (SAE J2743 report)
Touchscreen That Operators Actually Use
Real-world upgrade: Swapped resistive for capacitive screen after seeing gloves cause mis-taps
Memory hack: 500 programs? We allocate 50 slots to “John’s setup” / “Line 3 config” – because workers rename everything!
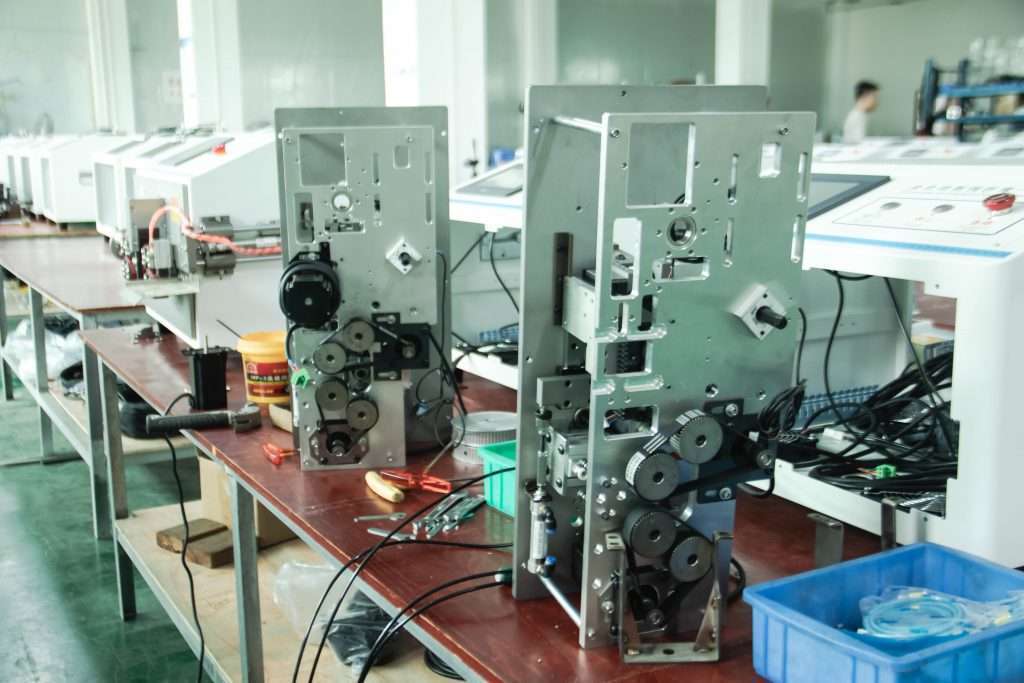
📐 Technical Specs Without the Marketing Fluff
Parameter Engineer’s Translation Wire Range 2-6 mm² “Means 1.8mm² works if pre-straightened, but 6.5mm² will jam the wheels” ≤0.002×L Precision “For a 500mm wire = ±1mm. Add ±0.3mm if your reel has tension spikes” Servo Four-wheel Drive “Solves the #1 pain: 2-4mm² silicone wires slipping during acceleration” 180–600 W Power “Draws 220W at 300pcs/hr – cheaper than your workshop lights”
🏭 Where This Machine Beats Manual Labor (Proven)
Medical Instrument Case
Global Medical Ltd. – Catheter Wiring Line
Old process: 3 stations (cut/strip → bend → QC) → 18% rework rate
With this machine:

Result: Rework ↓ to 1.2% – because human fingers no longer touch conductors
Automotive Harness Hell Fix
German EV Supplier – Door Harness Section
Pain point: 37 different bend angles across 2m wires → 5 operators constantly retooling
Our solution:
Pre-loaded 37 angle profiles into machine memory
Added QR code scanning to auto-select programs
ROI: Saved €11,200/month in labor + scrap reduction
⚙️ How It Works (Without the Brochure Jargon)
Feeding: Four servo wheels grip like “industrial fingers” – pressure adjustable from 0.5-6kg (no crushed shielding!)
Cutting: Blades move at 0.01mm/step to avoid conductor deformation
Bending:
Critical step: Wire gets heated to 65°C (via IR module) before bending copper-heavy cables
Secret sauce: Bending arm follows wire’s natural curvature to prevent kinking
“You’ll know it’s working when bends look like poured liquid metal.” – Our lead mechanic’s sign-off test
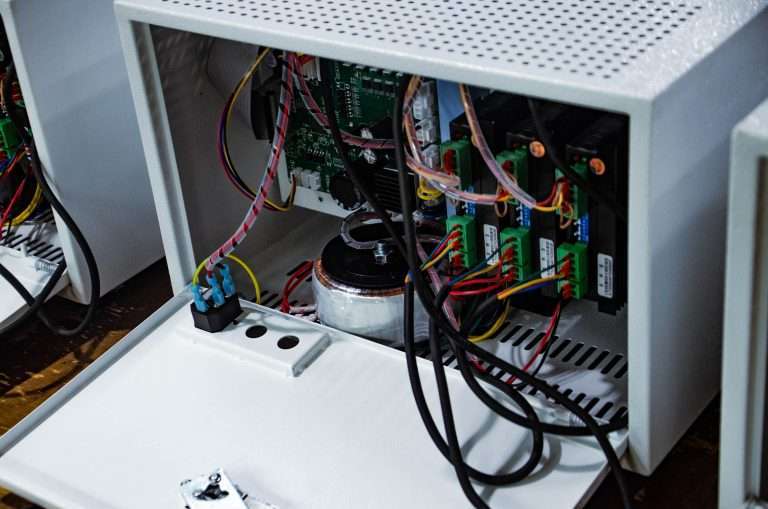
❓ FAQs We Get from Skeptical Engineers
Q: Can it handle flat ribbon cables?
*A: Yes, but use the optional V-groove wheels (Part# WG-FLAT6). Warning: Don’t try bending at 90° – 45° max to avoid delamination.*Q: How accurate REALLY is the bending?
*A: Run this test yourself:Program a 100mm wire with 3 bends
Measure 10 samples with calipers
Check variance – ours stays under ±0.15mm at our factory QC.*
Q: What’s the #1 cause of failure?
A: Not cleaning copper shavings! They jam the bending head. Fix: Blow compressed air into the blade slot every 8 hours (we include a nozzle).
🔩 Upgrade Options for Heavy Users
Laser Marking Module: Etch wire IDs directly after stripping (IPC/WHMA-A-620 compliant)
Anti-Static Kits: For medical/semiconductor work (tested to 10^6 Ω resistance)
Dust Extraction Port: Connects to your workshop vacuum (saves 2hr/day cleaning)
Engineer to Engineer Talk
“Look, if you’re bending over 200 wires/day – stop risking carpal tunnel from manual tools. This machine pays back in 4 months (we’ll send the ROI calc template).
Better yet: Send me your trickiest wire sample. We’ll process it here and film the results – no sales talk, just engineering.”
👉 [Email Me Your Specs]